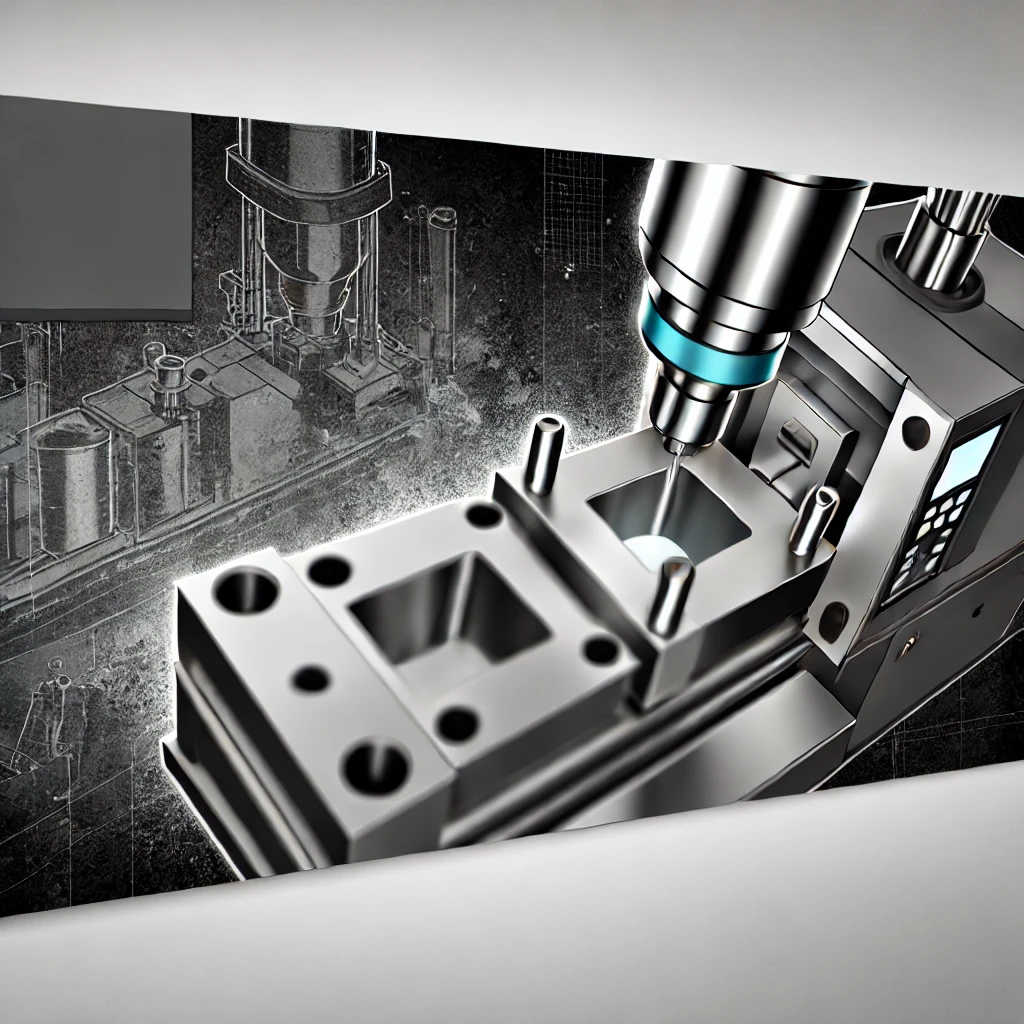
Understanding the Plastic Injection Moulding Process
Plastic injection moulding is a versatile manufacturing technique widely utilised across industries such as construction, engineering, and component parts production. Its adaptability allows for the creation of precision components from various materials, including metals (in processes like die-casting), glass, elastomers, and numerous plastics like thermoplastics and polymers.
Historical Context
The inception of injection moulding dates back to 1872 when American inventors John Wesley Hyatt and his brother, Isaac, patented the first injection moulding machine. This early device functioned similarly to a large hypodermic needle, forcing melted plastic through a heated cylinder into a shaped mould. Initial products manufactured using this method included buttons, collar stays, and hair combs. The demand for mass-produced, cost-effective items surged during the Second World War, further popularising this manufacturing process.
The Injection Moulding Process
The plastic injection moulding process involves several key steps:
1. Material Preparation: Raw plastic material, typically in the form of granules or pellets, is fed into a hopper.
2. Melting: The plastic is heated until it reaches a molten state.
3. Injection: The molten plastic is injected under pressure into a precisely designed mould cavity, which can be single or multi-cavity depending on the desired output.
4. Cooling: The moulded part is allowed to cool and solidify within the mould.
5. Ejection: Once solidified, the mould opens, and the finished component is ejected using mechanisms such as moving rods, plates, or air blasts.
The moulds are typically crafted from durable metals like steel or aluminium to withstand repetitive use and ensure the production of components that meet exact specifications.
Applications of Injection Moulded Parts
Injection moulding facilitates the production of parts in a vast range of sizes, from minute machine widgets to large items like car body panels. Common applications include packaging materials, automotive components, storage containers, toys, plumbing fixtures, and medical devices.
Advantages of Plastic Injection Moulding
Utilising plastic in injection moulding offers several benefits:
• Versatility: Plastics can be moulded into virtually any shape or size and are available in a wide array of colours.
• Durability and Hygiene: Plastic components are robust and maintain hygienic properties, making them suitable for various applications.
• Recyclability: Many plastics, such as thermoplastics, are recyclable, supporting sustainable manufacturing practices.
Advanced Injection Moulding Techniques
To achieve specific finishes or incorporate multiple materials, advanced methods like two-shot or multi-shot moulding are employed. These techniques allow for the integration of different materials into a single finished part, enhancing functionality and aesthetic appeal.
Considerations in Injection Moulding
While injection moulding is efficient, it requires meticulous maintenance of machinery and moulds to prevent production delays. Regular inspections and prompt repairs are essential to ensure consistent quality and efficiency in the manufacturing process.
By understanding and implementing the plastic injection moulding process effectively, manufacturers can produce high-quality, precision components suitable for a wide range of industrial applications.