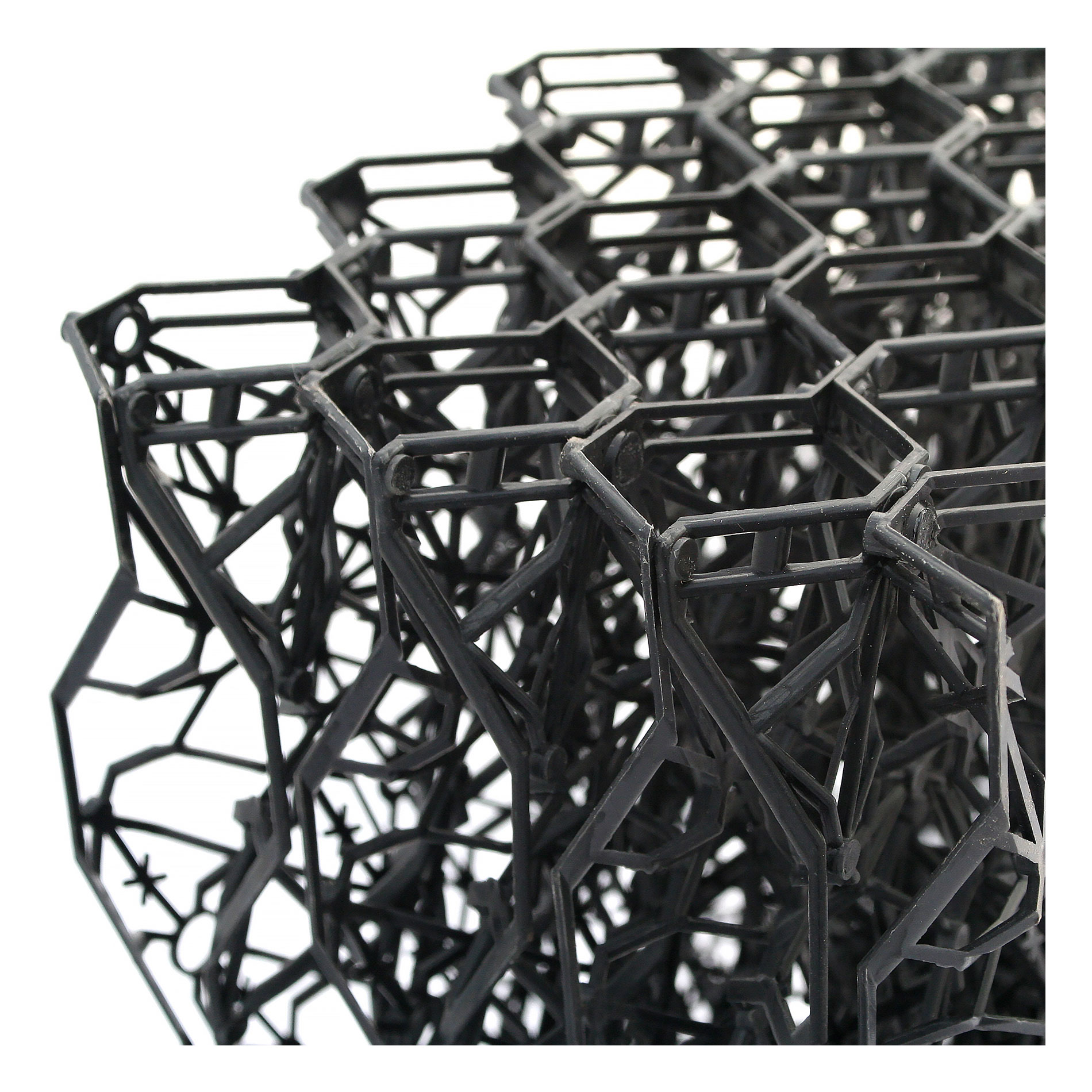
What is Plastic Injection Moulding?
Plastic injection moulding is a manufacturing process that allows businesses to produce hefty volumes of plastic goods. Injection moulding is used when you’re mass-producing consumer goods like kitchenware and even larger items, like trash bins. On the other hand, injection moulding is also ideal for non-consumer parts, like those with mechanical uses. This process permits businesses to swiftly produce a wide variety of plastic goods, helping you move efficiently from production to distribution.
What does the plastic injection moulding process entail?
The injection moulding process is simple and consists of four main steps:
1. The plastic material, known as thermoplastic, is melted so it can easily fill every crevice of its corresponding mold.
2. The molten plastic is injected into the metal mold.
3. The hot material is allowed time to cool and take its solid shape.
4. Once the plastic material has taken its solid shape, the hardened material is removed from the mold.
There are several types of thermoplastics which can be used for this process. Some of the most common include:
- Acrylonitrile Butadiene Styrene (ABS)
- Polypropylene
- Nylon
- Polyethylene
- Polycarbonates
These different kinds of thermoplastics are often shaped into pellets, which makes it easy for the injection molding process. Depending on the goods being produced, these pellets may be mixed with other recycled materials, pigments, and any other requested additives to achieve the intended final design.
How does plastic injection moulding help businesses?
Businesses benefit from the use of plastic injection moulding in several different ways, including:
Production Efficiency
Plastic injection moulding is incredibly fast, allowing businesses to mass produce their goods and meet consumer demand. A full injection molding cycle can take as little as a few seconds! Not only is the cycle speed impressive, but the cycle involves the production of several parts at once.
This combination between speed and output is what makes injection moulding a favorable process for businesses in a wide range of industries. From agriculture to building and construction to electronics and engineering, this process is a favorite and it’s not hard to see why.
Diminished Waste
Plastic injection moulding allows for efficient use of materials. The thermoplastic pellets are used to fill the desired mold instead of using large blocks of plastic to cut out a final product, as seen with computer numerical control (CNC) machining.
Quality Consistency
Molds make this process replicable, allowing for uniformity in product quality. Thousands (or millions!) of the same plastic parts can be produced in a single day and when they are all created with the same mold, you’ll notice consistency across the final products, which adds value to your branding.
Overall Savings
Molds allow you to use precision when using thermoplastics, so even if there is leftover material, it is still significantly less waste than other manufacturing processes. Plus, any leftover plastic can easily be reused or sold to manufacturers that make use of those recycled bits.
If you’re looking to scale production drastically, plastic injection moulding is a no-brainer for your business.